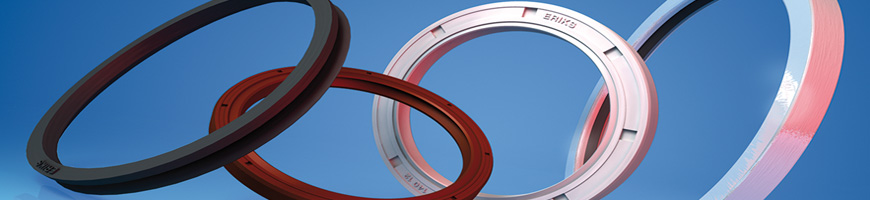
How to select the right oil seal
One of the most used seals in technology is the oil seal. This is generally implemented as a zero pressure seal of lubricating oil and grease on a rotating shaft.
It is sometimes also used for other liquids and gases and for solids in the form of powder or granules. The seal keeps both the grease inside the application and any dirt outside of it with the addition of a dust lip.
The main causes of lubricant leaking from pumping systems, hydraulic machines or gearcases are the wrong selection,
improper application, inadequate installation and insufficient maintenance practices of sealing systems.
These problems can be avoided through a better understanding of the types of sealing materials available,
proper application and maintenance practices.
To help you easily select the right seal for your application, we have compiled in this article some useful tips and explanations of oil seals parameters.
What to look for when selecting an oil seal
When choosing an oil seal for an application, selecting the correct elastomer is important for maintaining good seal life and avoiding leakage or other damage. Consider the following points when making your purchase:
- Under lip temperature caused by friction
- Shaft speed
- Temperature of the medium (depends on the right material)
- Chemical influence of the medium (depends on the right material)
- Pressure on the seal
Be sure to also review the guidelines regarding hardware conditions such as shaft hardness and shaft roughness.
Choice of material
Oil seals are used in many manufacturing industries. With such a broad range of materials available, it can be tricky to select the appropriate material for a certain application. We have compiled the most important facts about different oil seals material so that the choice of the correct oil seal becomes easier for our customers.
Material lip
In the standard construction, oil seals are made from oil and grease resistant rubber based on NBR (Perbunan). This material has very good running properties and excellent wear resistance. For high shaft speeds, large radialtolerances and good chemical resistance a range of other rubber materials is available at ERIKS.
Material overview for oil seals:
Rubber type | Material Code ISO 1629 | Heat resistance |
---|---|---|
Nitrile High wear resistance good running properties for general use |
NBR | -35 °C to + 100 °C |
Polyacrylate Better heat, oil and chemical resistance than NBR It is recommended for use in oil which contains load bearing additives such as EP gear oils |
ACM | -20 °C to + 130 °C |
Viton® High level of chemical resistance High temperature resistance |
FPM | -15 °C to + 180 °C |
Silicone Wide temperature range Commonly used in low temperature applications Very prone to mechanical damage during fitting |
MVQ | -50 °C to + 150 °C |
Polytetrafluoroethylene Chemical resistant Low coefficient of friction poor elastic properties not wear resistant if used by dynamic applications |
PTFE | -80 °C to + 200 °C |
Leather Recommended for abrasive applications Good running properties, due to the impregnated seal lip Can be used on shafts which have a surface roughness outside the range for rubber seals Not suitable for water |
- | -40 °C to + 90 °C |
The different elastomers of oil seals are also different in their resistance to certian media. In the following table you can see which elastomer is suitable for which temperature ranges of the sealing medium:
Elastomer | Min.Temp. | Motor Oil | Gearbox oil SAE | ATF Oil | Hypoid Oil | Grease | Fuel | Water | Logen | Brake Fluids |
---|---|---|---|---|---|---|---|---|---|---|
NBR | -35 | 100 | 80 | 100 | 80 | 90 | 90 | 70 | 70 | - |
ACM | -20 | 130 | 120 | 130 | 120 | * | * | - | - | - |
MVQ | -50 | 150 | 130 | * | - | * | * | - | - | - |
FPM | -30 | 180 | 150 | 170 | 150 | * | 150 | 100 | 100 | * |
- (minus in table) = For these media the elastomer is not resistant
* (star in table)= Within these groups, there are media which can be sealed by the elastomer in question. although these media could have a disadvantageous influence on the elastomer
Material surface
ERIKS oil seals are constructed with either a rubber case or a metal case.
Rubber
Rubber-cased oil seals are the most common oil seal execution, used when a metal-cased seal has the potential to fail. In high temperatures and high pressures, fast expanding rubber can provide a tight fit and more stable sealability. Rubber-cased oilseals are frequently used as replacement for metal-cased oilseals in MRO applications because of easier installation. The most popular rubber-cased seal is Type R.
Metal
Metal-cased oil seals are used when installed to a housing bore made of the same material. This allows for equal contraction and expansion of the materials during operation, preventing leakage from occurring. Typically metal-cased seals are more cost efficient than rubber seals, but if the case material and housing bore material are not the same, a rubber seal should be used instead. The most popular metal-cased seal is Type M.
Spring material
Springs can be made from different materials such as carbon steel or stainless steel including 304 and 316. Spring steel is often used as material name, refers to carbon steel, and is known for its pliability and strength.
Pressure resistance
Maximum static pressure
An oil seal is principally intended for operating under normal atmospheric conditions. If however the peripheral speed does not exceed 8 metres per second, the oil seal is able to withstand a pressure of ca. 0,5 bar.
Oil seals with a large shaft diameter (500 mm) the pressure which the oil seal may be exposed to is 0,1 bar.The permissible pressure greatly depends on the operating conditions such as shaft speed, temperature and lubrication.
If the actual pressure exceeds the permissible maximum, the lip of the oil seal is forced against the shaft, resulting in a higher radial load, a higher level of friction, and excessive wear of shaft and seal.
To balance the pressure, oil seals can be provided with a supported sealing lip by using an easily fabricated metal support ring. Oil seals with a supported sealing lip can be used on small diameter shafts for pressures up to 6 bar if conditions are favourable (low temperatures, relatively low speed, good lubrication)
How to measure parametres such as diameter and width
Oil seal sizes are typically specified by three common dimensions: the rotating shaft diameter (sometimes referred to as the inside diameter of the seal),
the housing bore diameter (also called the outside diameter of the seal), and the housing width (thickness) of the seal itself.
Because of an oil seal’s purpose, the right size is crucial.
The inside diameter of the oil seal must always be slightly smaller than the shaft diameter in order to seal lubricants inside and prevent harmful contamination.
In order to find the right oil seal, one needs to know parametres such as the diameter of the shaft and the housing or the width of the housing - these parametres are all measured in mm. The following images help to identify which part of the oil seals has to be measured to know these parametres.
Maximum shaft speed
This is the fastest speed the seal can support without potential failure.
The maximum allowable shaft speed is a function of the shaft finish, runout, housing bore and shaft concentricity,
type of fluid being sealed and the type of oil seal material.
When speed surpasses a seal's limit,
the sealing lip can experience excessive wear and tear due to the increased friction.
This wearing can negatively impact a seal's service life, and lead to oil leaks and machine downtime. The maximum shaft speed is measured in m/s.